Auch der Betreiber einer Maschine hat Pflichten
Die Sicherheit am Arbeitsplatz ist ein zentrales Anliegen in der Industrie. Maschinenbetreiber tragen eine entscheidende Verantwortung, um Gefahren zu minimieren und die Sicherheit ihrer Mitarbeiter zu gewährleisten. Zu den wichtigsten Betreiberpflichten gehört die regelmäßige Prüfung der vorhandenen Schutzmaßnahmen. Dieser Artikel beleuchtet die rechtlichen Grundlagen, die Bedeutung dieser Prüfungen sowie die praktischen Schritte zur Umsetzung.
Rechtliche Grundlagen
In Deutschland sind die Betreiberpflichten für Maschinenbetreiber im Rahmen des Arbeitsschutzgesetzes (ArbSchG) und der Betriebssicherheitsverordnung (BetrSichV) festgelegt. Diese Vorschriften verlangen von den Betreibern, dass sie sicherstellen, dass Maschinen und Anlagen sicher betrieben werden können. Hierzu zählen die Implementierung von Schutzmaßnahmen sowie deren regelmäßige Überprüfung.
Laut § 3 BetrSichV sind Arbeitgeber verpflichtet, die Gefährdungen zu ermitteln und geeignete Schutzmaßnahmen zu treffen. Diese Maßnahmen müssen regelmäßig auf ihre Wirksamkeit überprüft werden. Dies beinhaltet sowohl technische Schutzmaßnahmen (z. B. Schutzeinrichtungen) als auch organisatorische Maßnahmen (z. B. Schulungen).
Haben Sie z.B. eine kollaborierende Roboteranwendung in Ihrem Unternehmen, so sind Sie verpflichtet, die Wirksamkeit der Kollisionserkennung durch jährliche Wiederholungsmessungen zu prüfen und zu dokumentieren. Nutzen Sie Laserscanner oder Lichtgitter, so müssen Sie einmal pro Jahr prüfen, ob die Reaktions- und Anhaltezeit der Maschine noch den Anforderungen entspricht. Sie müssen eine jährliche Stoppzeit und Stoppwegmessung durchführen.
Bedeutung der regelmäßigen Prüfungen
Die regelmäßige Prüfung von Schutzmaßnahmen ist entscheidend, um die Sicherheit der Mitarbeiter zu gewährleisten. Maschinen unterliegen Abnutzungs- und Alterungsprozessen, die ihre Sicherheit beeinträchtigen können. Ein Beispiel ist die Abnutzung von Schutzeinrichtungen, die den Zugang zu gefährlichen Bereichen der Maschine verhindern sollen.
Durch regelmäßige Prüfungen können Betreiber:
- Sicherheitsrisiken frühzeitig erkennen: Potenzielle Gefahren können identifiziert und behoben werden, bevor es zu Unfällen kommt.
- Rechtlichen Verpflichtungen nachkommen: Die Nichteinhaltung der Prüfpflichten kann rechtliche Konsequenzen nach sich ziehen, einschließlich Bußgeldern oder Haftung für Unfälle.
- Das Vertrauen der Mitarbeiter stärken: Ein sicheres Arbeitsumfeld fördert das Vertrauen und die Motivation der Mitarbeiter, was sich positiv auf die Produktivität auswirkt.
Praktische Umsetzung der Prüfungen
Um die Verpflichtungen zur regelmäßigen Prüfung der Schutzmaßnahmen effektiv umzusetzen, sollten Betreiber folgende Schritte in Betracht ziehen:
- Erstellung eines Prüfplans: Definieren Sie einen klaren Zeitrahmen für die Prüfungen basierend auf der Art der Maschinen und den spezifischen Risiken.
- Dokumentation: Führen Sie Protokolle über durchgeführte Prüfungen, festgestellte Mängel und durchgeführte Maßnahmen. Dies dient nicht nur der Nachverfolgbarkeit, sondern kann auch als Nachweis bei Audits oder Inspektionen dienen.
- Schulung der Mitarbeiter: Stellen Sie sicher, dass alle Mitarbeiter, die mit den Maschinen arbeiten, über die sicherheitsrelevanten Aspekte informiert sind und wissen, wie sie Schutzmaßnahmen überprüfen können.
- Zusammenarbeit mit Fachleuten: In vielen Fällen kann es sinnvoll sein, externe Fachleute hinzuzuziehen, um die Prüfungen durchzuführen oder die Betreiber bei der Umsetzung von Sicherheitsmaßnahmen zu unterstützen.
Fazit
Die regelmäßige Prüfung von Schutzmaßnahmen ist eine essentielle Betreiberpflicht, die sowohl rechtliche als auch praktische Dimensionen hat. Durch die Implementierung eines strukturierten Prüfprozesses können Maschinenbetreiber nicht nur gesetzliche Anforderungen erfüllen, sondern auch aktiv zur Sicherheit am Arbeitsplatz beitragen. Ein sicheres Arbeitsumfeld ist nicht nur ein rechtliches Gebot, sondern auch ein fundamentaler Bestandteil erfolgreicher Unternehmensführung.
Sie haben Fragen zu diesem Thema oder benötigen Unterstützung bei der Umsetzung Ihrer Betreiberpflichten. Gerne bieten wir Ihnen eine jährliche Prüfung Ihrer Schutzmaßnahmen an. Wir führen die geforderten Kraft- und Druckmessungen an Ihrer kollaborierenden Roboterapplikation durch und Messen die Wirksamkeit Ihrer Laserscanner und Lichtgitter im Rahmen einer Stoppzeit und Stoppwegmessung. Sprechen Sie uns gerne an.

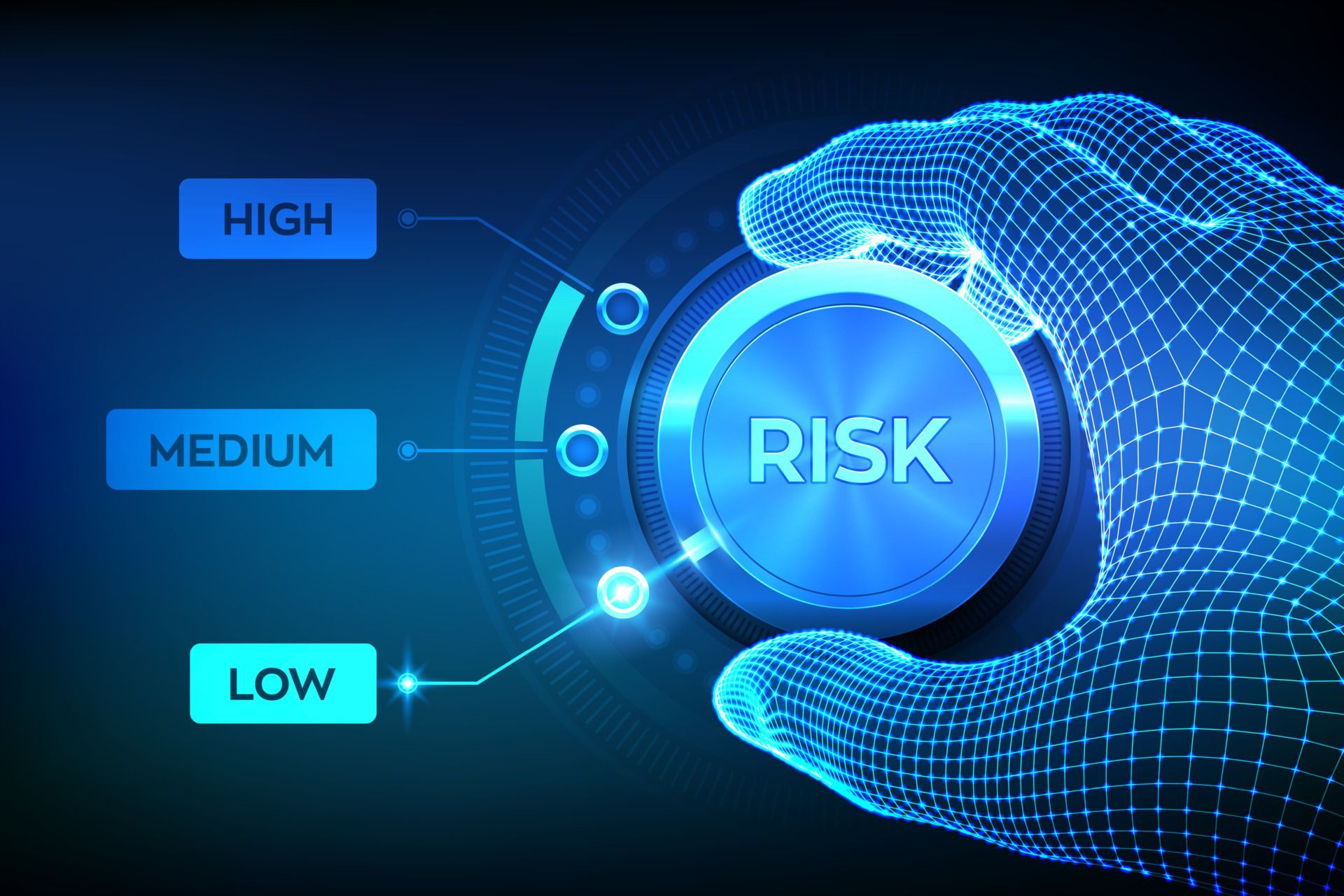
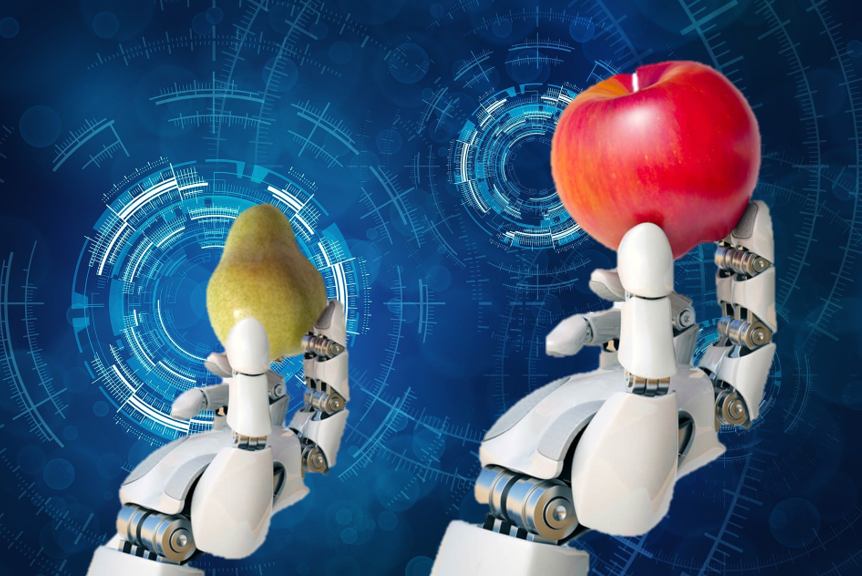