Risikobeurteilung vs. Gefährdungsbeurteilung
Risikobeurteilung vs. Gefährdungsbeurteilung
In der heutigen Arbeitswelt sind Sicherheit und Gesundheitsschutz von größter Bedeutung. Zwei zentrale Konzepte in diesem Kontext sind die Risikobeurteilung und die Gefährdungsbeurteilung. Beide dienen dem Ziel, Risiken am Arbeitsplatz zu identifizieren und zu minimieren, verfügen jedoch über unterschiedliche Schwerpunkte und rechtliche Grundlagen.
Definitionen
Risikobeurteilung: Die Risikobeurteilung ist ein umfassender Prozess, der darauf abzielt, die potenziellen Risiken in einem bestimmten Kontext zu identifizieren, zu analysieren und zu bewerten. Dabei wird sowohl die Wahrscheinlichkeit des Eintretens eines Risikos als auch dessen mögliche Auswirkungen auf Menschen, Umwelt und Vermögenswerte betrachtet.
Gefährdungsbeurteilung: Die Gefährdungsbeurteilung ist ein systematisches Verfahren zur Identifizierung und Bewertung von Risiken für Menschen, Eigentum und die Umwelt.
Die Gefährdungsbeurteilung kann nach normativen Beurteilungskriterien (z. B. Grenzwerte) und/oder nach subjektiven Beurteilungskriterien (z. B. Eintrittswahrscheinlichkeit, voraussichtliche Schwere eines möglichen Gesundheitsschadens) erfolgen. Gefährdungsbeurteilungen sind für ein definiertes Arbeitssystem vorzunehmen.
Die Beurteilung der einzelnen Arbeitssysteme ist die Grundlage zur Erfüllung der Forderung gem. § 5 Arbeitsschutzgesetz (ArbSchG), wonach der Arbeitgeber eine Beurteilung der Arbeitsbedingungen aller Beschäftigten je nach Art ihrer Tätigkeit durchzuführen hat. Die Gefährdungsbeurteilung ist somit ein Handlungsinstrument, mit dem
- Handlungsschwerpunkte bestimmt,
- betriebliche Aktivitäten der Verbesserung des Arbeitsschutzes zielorientiert gesteuert und
- Arbeitsschutzaktivitäten kontrolliert sowie auf ihre Wirksamkeit hin beurteilt werden können.
Wer muss welche Durchführung?
Hersteller: Der Hersteller ist in der Regel für die Risikobeurteilung verantwortlich, insbesondere wenn es um die Sicherheitsprüfung von Maschinen, Geräten oder Produkten geht. Gemäß der Maschinenrichtlinie (2006/42/EG) ist er verpflichtet, eine Risikobeurteilung durchzuführen, um sicherzustellen, dass das Produkt sicher in den Verkehr gebracht werden kann.
Betreiber: Der Betreiber hingegen ist für die Gefährdungsbeurteilung zuständig. Dies betrifft alle Arbeitgeber, die verpflichtet sind, eine Gefährdungsbeurteilung zu erstellen, um die Sicherheit am Arbeitsplatz zu gewährleisten. Diese Verantwortung ist im Arbeitsschutzgesetz (ArbSchG) verankert.
Wann muss eine Beurteilung durchgeführt werden?
Risikobeurteilung: Eine Risikobeurteilung muss immer dann durchgeführt werden, wenn eine neue Maschine erstellt oder an einer bereits bestehenden Maschine eine wesentliche Veränderung vorgenommen wird (letzteres ist im Interpretationspapier des BMAS "Wesentliche Veränderung" vom April 2015 geregelt. Dieses Dokument finden Sie hier.).
Wichtig dabei ist, dass die Risikobeurteilung ein entwicklungsbegleitender Prozess sein sollte und nicht erst nach Aufbau der Maschine erstellt wird. Dies hilft nicht nur dabei die Maschine sicher zu konstruieren und zu bauen, sondern erspart dem Hersteller auch unnötige Kosten.
Gefährdungsbeurteilung: Eine Gefährdungsbeurteilung muss jedes Mal durchgeführt werden, wenn neue Arbeitsmittel, Arbeitsprozesse und Arbeitsverfahren eingesetzt werden, die möglicherweise ein Gesundheits- oder Sicherheitsrisiko für die Beschäftigten bergen. Gefährdungsbeurteilungen sollten zudem regelmäßig durchgeführt werden, damit bestehende Gefährdungen überwacht, kontrolliert und gesteuert werden können. Über die gesetzliche Verpflichtung zur Durchführung von Gefährdungsbeurteilungen nach ArbSchG hinaus sollen Gefährdungsbeurteilungen insbesondere dann durchgeführt werden, wenn
- bei Planung oder Änderung von Arbeitsplätzen, Anlagen und Verfahren Entscheidungshilfen im Sinne der Sicherheit und des Gesundheitsschutzes benötigt werden
- auf Grund von Hinweisen oder bekannt gewordener Beinahe-Unfälle auf besondere Gefährdungssituationen zu schließen ist
- sich besondere Unfall- oder Gesundheitsbelastungen an bestimmten Arbeitsplätzen, bei bestimmten Arbeitsverfahren oder Tätigkeiten zeigen
- bei Überprüfungen der Arbeitsplätze festgestellt wird, dass Arbeitsschutzmaßnahmen nicht mehr ausreichend wirksam sind.
Rechtliche Grundlagen
Risikobeurteilung: Die rechtliche Grundlage für die Durchführung der Risikobeurteilung liegt vor allem in der Maschinenrichtlinie, die spezifische Anforderungen für Hersteller von Maschinen und Anlagen vorgibt. Weitere relevante Normen sind die ISO 12100 (Sicherheit von Maschinen) und verschiedene Produktsicherheitsgesetze.
Gefährdungsbeurteilung: Die Gefährdungsbeurteilung ist gesetzlich im Arbeitsschutzgesetz (ArbSchG) und in der Unfallverhütungsvorschrift (UVV) festgeschrieben. Arbeitgeber sind verpflichtet, Gefährdungen am Arbeitsplatz zu identifizieren, zu bewerten und geeignete Maßnahmen zur Risikominderung abzuleiten.
Regulierungen
Die Verfahren für die Durchführung der Gefährdungsbeurteilung sind in der Technischen Regel für Arbeitsstätten (ASR A2.2) und in den Vorschriften der Deutschen Gesetzlichen Unfallversicherung (DGUV) detailliert beschrieben. Für die Risikobeurteilung existieren Normen und Leitlinien, die je nach Branche und Art des Produkts variieren. Im Bereich Maschinenbau ist hier insbesondere die EN ISO 12100 als Norm zu nennen.
Gemeinsamkeiten und Unterschiede
Gemeinsamkeiten:
- Beide Beurteilungen verfolgen das gemeinsame Ziel, Risiken und Gefahren zu identifizieren, um die Gesundheit und Sicherheit von Personen zu schützen.
- Sowohl Risikobeurteilung als auch Gefährdungsbeurteilung erfordern eine systematische Analyse und Dokumentation.
- Sie müssen regelmäßig aktualisiert werden, um Veränderungen im Arbeitsumfeld oder bei Produkten zu berücksichtigen.
Unterschiede:
- Fokus: Die Risikobeurteilung betrifft die Gesamtheit der Risiken eines Produktes oder Prozesses, während die Gefährdungsbeurteilung spezifisch auf Gefahren am Arbeitsplatz abzielt.
- Verantwortlichkeit: Die Verantwortung für die Risikobeurteilung liegt beim Hersteller, während der Betreiber für die Durchführung der Gefährdungsbeurteilung verantwortlich ist.
- Rechtliche Anforderungen: Die Risikobeurteilung ist spezifisch notwendig für Produkte und wird durch Produktsicherheitsgesetze geregelt, während die Gefährdungsbeurteilung allgemeine Anforderungen für alle Arbeitgeber darstellt.
Fazit
Risikobeurteilung und Gefährdungsbeurteilung sind komplementäre Instrumente im Arbeitsschutz. Während die Risikobeurteilung beim Hersteller ansetzt und auf die Sicherheit von Produkten fokussiert, ist die Gefährdungsbeurteilung essenziell für Betreiber, die ein sicheres Arbeitsumfeld gewährleisten müssen. Ein integrierter Ansatz, der beide Beurteilungen berücksichtigt, ist entscheidend für die Minimierung von Risiken und die Förderung der Sicherheit in der Arbeitswelt.
Sie haben Fragen zur Risikobeurteilung oder zur Gefährdungsbeurteilung? Wir können Ihnen bei beiden helfen. Wir führen sowohl Risikobeurteilungen für Hersteller von Maschinen als auch Gefährdungsbeurteilungen für Betreiber durch. Ebenso schulen wir Sie gerne in diesen Bereichen. Sprechen Sie uns gerne an!

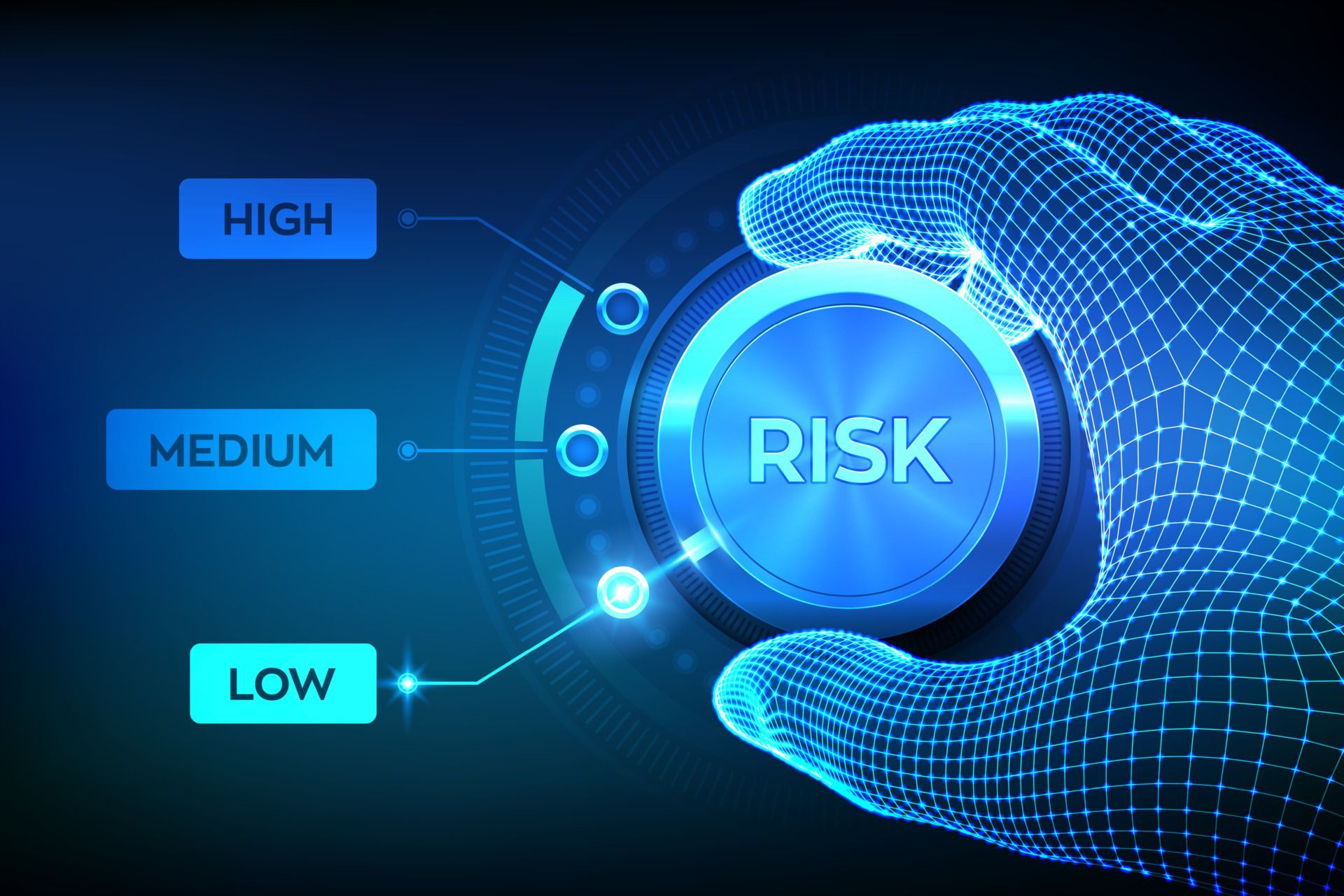
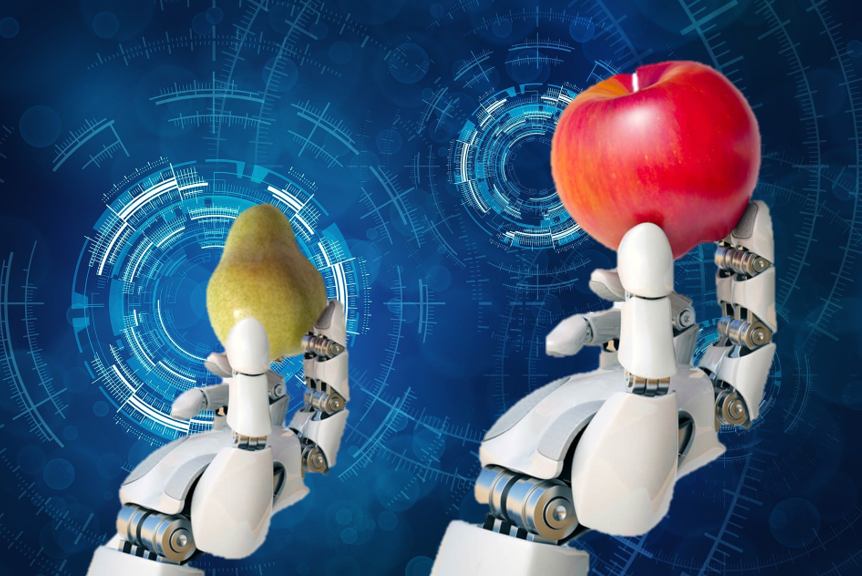